How to Choose a Warehouse Facility
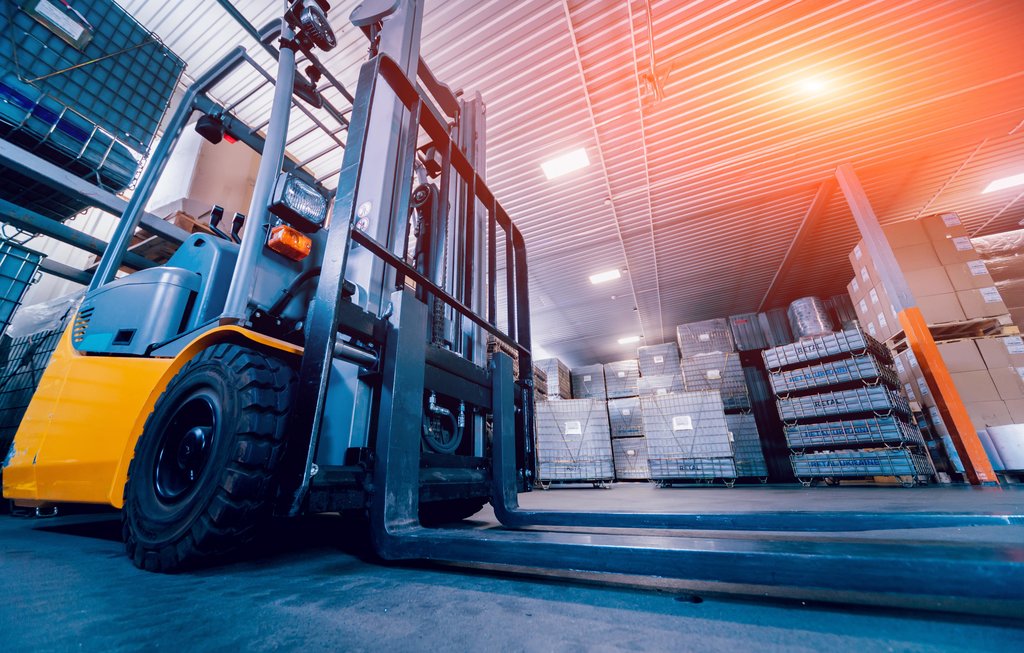
A wide range of businesses require warehousing when it comes to transporting products and goods across Europe and beyond, we take you through how to choose a warehouse facility that suits yoru business needs.
A critical part of the landside supply chain, businesses can use warehousing as the last stop before products are sent to the distribution centre or the first point before products are shipped overseas.
Regardless of why a business might require warehousing, there are certain key things they should look for when finding a warehouse and logistics partner.
We look at each in more detail below:
Quality of warehousing offered:
Businesses should only work with logistics and storage partners that can provide modern warehousing that is fit for purpose, especially when it comes to security.
Warehouses must be able to protect products from the elements and they must be watertight and dry. If not, goods can become damp and damaged.
The best warehouse facilities will also use state of the art technologies that can be integrated with a business’s own systems and processes to monitor and manage storage.
In addition, technology is used to provide clear visibility to stock levels which in turn allows for effective and efficient planning of shipments and deliveries.
Wireless scanning technologies are often deployed by the storage provider to make it easier to find products, reducing the time it takes to load them onto trailers for shipping.
Finally, check to see if the warehouse is accredited – this is particularly important if you are storing food products. If you are, look for British Retail Consortium (BRC) or AIB accreditation.
Good transport links:
The location of the warehouse is equally important, particularly when it comes to transport links as you want your products to be dispatched without delay.
Consider whether the location of the storage facility has good access to your key market. If that is Europe, you may wish to work with a facility that is close to a port such as Hull.
Road, rail and waterways links are just as important. If the facility is not close to the major motorway and rail networks then the time taken to deliver your products can increase significantly.
If your goods will be transported further afield you may prefer to work with a warehousing provider that has easy access to cargo and freight airport terminals.
Transportation services:
The next thing to think about is whether the warehouse provider also offers transportation services. If they do, this can significantly streamline the process and reduce costs.
In most cases, transportation will be via trailer so consider the different types of trailer the logistic firm has to offer. Double Deck and Mega trailers are the most common.
If you are a smaller business it is certainly worth working with a warehouse and logistics partner that provides groupage services.
This is the practice of grouping together smaller shipments going to the same destination so that businesses only pay for the part of the trailer they use.
This can reduce storage costs as goods can be transported more regularly instead of waiting for a large enough order to require a full trailer.
A good reputation:
It goes without saying that you should only partner with a warehouse and logistics provider that has a good reputation and can provide the best possible solution to meet your needs.
This can sometimes mean paying more, but when you consider the importance of safely storing your products, and shipping them to the required destination on time, it is a price worth paying.